Step-by-Step Guide: Commercial Roof Installation Process
The Critical Importance of a Well-Installed Commercial Roof

A commercial roof serves as the first line of defense for your entire building. It shields your property, inventory, and personnel from the elements, ensuring smooth business operations. A properly installed commercial roof offers numerous benefits:
- Protection: It safeguards the building structure, its contents, and occupants from rain, snow, wind, and other external factors.
- Durability: A well-installed roof extends its lifespan significantly, minimizing the need for frequent repairs or costly replacements.
- Energy Efficiency: Proper installation ensures optimal insulation, reducing energy consumption for heating and cooling.
- Property Value: A well-maintained roof enhances the overall value and marketability of your commercial property.
Commercial Roof Installation Overview
Installing a commercial roof involves a meticulous process:
- Inspection & Preparation: A thorough inspection assesses the existing roof structure, identifying any potential issues. The surface is then prepped for the new installation.
- Material Selection: Choosing the appropriate roofing materials (metal, built-up roofing, etc.) depends on factors like budget, desired lifespan, and local climate.
- Underlayment & Insulation: Installation of an underlayment provides a water-resistant barrier, followed by insulation for improved energy efficiency.
- Membrane Installation: The chosen roofing membrane (sheets, shingles, etc.) is meticulously laid according to the material’s specifications.
- Flashing & Sealants: Flashing around penetrations like vents and pipes ensures watertight seals, preventing leaks.
- Final Touches: Final inspections, clean-up, and warranty registration complete the process.
Remember, proper installation by qualified professionals is crucial for maximizing the lifespan, performance, and overall value of your commercial roof.
Installing a commercial roof involves a meticulous process:
- Inspection & Preparation: A thorough inspection assesses the existing roof structure, identifying any potential issues. The surface is then prepped for the new installation.
- Material Selection: Choosing the appropriate roofing materials (metal, built-up roofing, etc.) depends on factors like budget, desired lifespan, and local climate.
- Underlayment & Insulation: Installation of an underlayment provides a water-resistant barrier, followed by insulation for improved energy efficiency.
- Membrane Installation: The chosen roofing membrane (sheets, shingles, etc.) is meticulously laid according to the material’s specifications.
- Flashing & Sealants: Flashing around penetrations like vents and pipes ensures watertight seals, preventing leaks.
- Final Touches: Final inspections, clean-up, and warranty registration complete the process.
Remember, proper installation by qualified professionals is crucial for maximizing the lifespan, performance, and overall value of your commercial roof.
Planning and Preparation: The Foundation of a Successful Roofing Project
Before embarking on any roofing work, meticulous planning and preparation are crucial for ensuring a smooth and successful installation process. This stage involves three key steps:
Site Assessment and Inspection
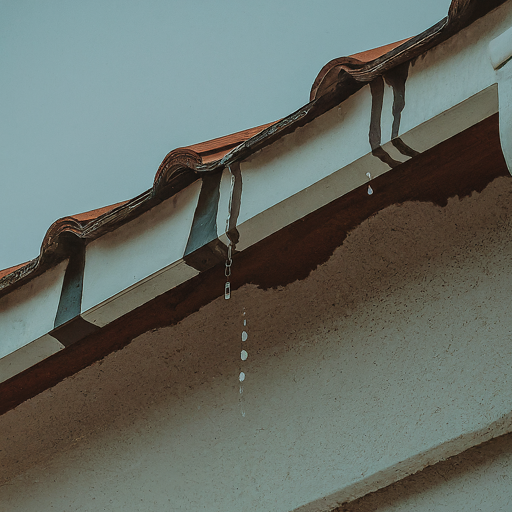
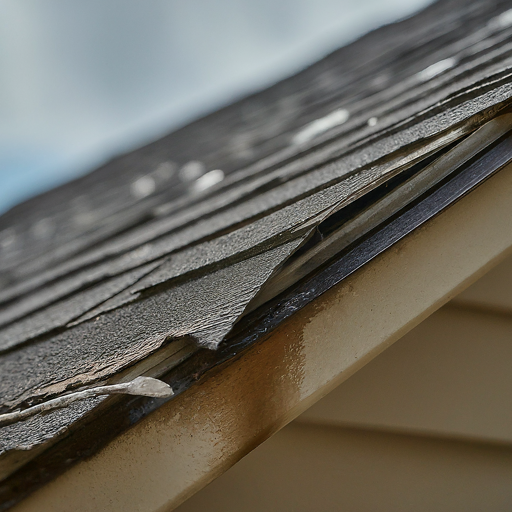
A thorough roof inspection by a qualified professional is paramount. This involves a detailed examination of the existing roof structure, identifying any potential damage signs that could compromise its integrity. Common signs of damage include:
- Visible Leaks or Water Stains: These indicate breaches in the roof’s watertightness, potentially leading to structural issues.
- Cracked, Sarped, or Missing Shingles/Membrane: This exposes the underlying structure to the elements, accelerating deterioration.
- Excessive Wear and Tear: Over time, even the most durable roofs succumb to natural aging. Early detection allows for timely repairs or a planned roof replacement before significant roof damage occurs.
By understanding the current condition of your roof, you can make informed decisions about the necessary course of action, whether it’s minor repairs, a partial roof replacement, or a complete overhaul.
Choosing the Right Materials and Equipment
Selecting the appropriate materials for your commercial roof is essential for optimal performance and longevity. Factors like budget, desired lifespan, local climate, and building code requirements all play a crucial role in this decision. Common commercial roofing materials include:
- Metal Roofing: Known for its durability and longevity, it’s ideal for areas with harsh weather conditions.
- Built-up Roofing (BUR): A multi-layered system offering excellent water resistance and fire protection.
- Single-ply Membranes: Lightweight and energy-efficient, these are popular choices for flat roof.
Choosing the right equipment for the installation process is equally important. This includes specialized tools like safety harnesses, hoists, and specialized cutting equipment, ensuring the safety and efficiency of the crew.
Obtaining Necessary Permits and Permissions
Before commencing any roofing work, obtaining the necessary permits and permissions from local authorities is mandatory. This ensures compliance with building codes and safety regulations, preventing potential delays or legal ramifications. The specific permits required may vary depending on the scope of the project and local regulations.
By prioritizing thorough planning and preparation, including a comprehensive roof inspection, material selection, and permit acquisition, you lay the groundwork for a successful and long-lasting roof care project. This meticulous approach minimizes the risk of unforeseen complications and ensures your commercial property receives the best possible protection.
Safety Measures: The Cornerstone of a Successful Commercial Roofing Project
In the realm of commercial roofing, safety reigns supreme. Ensuring a safe installation process goes beyond simply following protocols; it’s a fundamental responsibility that safeguards the well-being of workers and the overall success of the project.
Here’s why prioritizing safety measures is paramount:
- Preventing Injuries: Falls from heights, exposure to hazardous materials, and equipment malfunctions are all potential risks inherent in repair maintenance, and installation processes. Implementing robust safety measures significantly minimizes the chance of accidents and injuries.
- Reduced Costs: Accidents lead to downtime, medical expenses, and potential lawsuits. A strong safety culture fosters a proactive approach, preventing costly disruptions and ensuring project completion within budget.
- Enhanced Productivity: When workers feel safe and secure, they can focus on their tasks with greater confidence and efficiency, leading to a more productive installation process.
Several key elements contribute to a safe commercial roofing environment:
- Equipment Safety Checks: Regular inspections and maintenance of ladders, hoists, power tools, and other equipment ensure their proper functioning and minimize the risk of mechanical failures.
- Training and Certification: Installation teams must undergo comprehensive training on fall protection, hazard identification, safe work practices, and the proper use of personal protective equipment (PPE). Certifications like OSHA 30-Hour Construction Safety and Health demonstrate a commitment to safety standards.
Here are some of the top 10 safety measures in commercial roofing:
- Fall Protection: Implementing guardrails, safety nets, and personal fall arrest systems is crucial on all roofs with unprotected edges.
- Personal Protective Equipment (PPE): Hard hats, safety glasses, gloves, and slip-resistant boots are essential for protecting workers from falling debris, harmful materials, and weather elements.
- Ladder Safety: Proper ladder placement, secure footing, and the use of a spotter are vital for preventing falls while accessing the roof.
- Weather Monitoring: Suspending work during inclement weather, like high winds or heavy rain, minimizes the risk of slips and falls.
- Proper Ventilation: Adequate ventilation is essential when working with materials that emit harmful fumes or dust.
- Housekeeping: Maintaining a clean and clutter-free work environment prevents tripping hazards and facilitates safe movement.
- Emergency Preparedness: Having a readily available first-aid kit and clear emergency response protocols ensures prompt action in case of accidents.
- Underlayment Selection: Choosing the right underlayment, like an ice and water barrier, provides additional protection against moisture infiltration and potential falls.
- Insulation Safety: Wearing appropriate PPE and using safe handling techniques are crucial when working with insulation materials.
- Coverboard Safety: Securely installing coverboards prevents falls through openings and protects workers from exposed roofing elements.
By prioritizing a culture of safety and implementing these essential measures, commercial roofing companies can create a secure environment for their teams, ensuring a smooth and successful installation process that contributes to the overall sustainability and positive trends within the industry.
Commercial Roofing Installation Techniques: Choosing the Right Approach
The vast landscape of commercial roofing offers a diverse range of installation techniques, each with its unique advantages and disadvantages. Selecting the optimal approach hinges on factors like building type and budget. Here’s a breakdown of some common techniques:
Membrane roofing
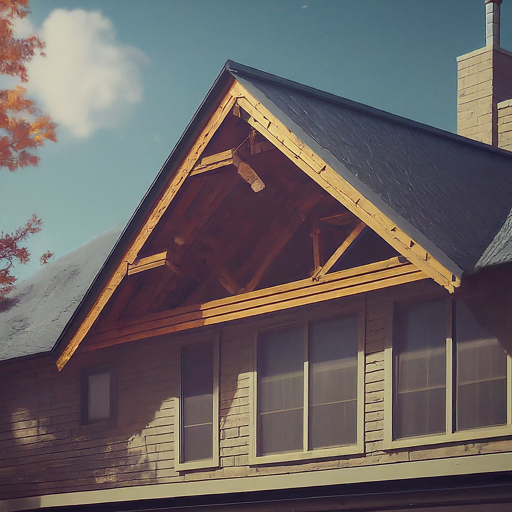
- Types: Single-ply (TPO, EPDM, PVC), Modified Bitumen (BUR)
- Advantages: Lightweight, energy-efficient, highly water-resistant, good for flat roofs.
- Disadvantages: May require specialized installation, susceptible to punctures, potential for wind uplift.
Asphalt roofing
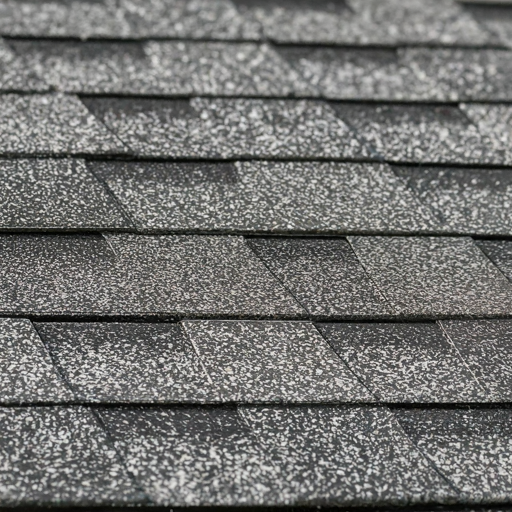
- Types: Shingles, Built-up Roofing (BUR).
- Advantages: Affordable, readily available, familiar installation process.
- Disadvantages: Susceptible to wind damage, shorter lifespan compared to other options, requires regular maintenance.
Metal roofing
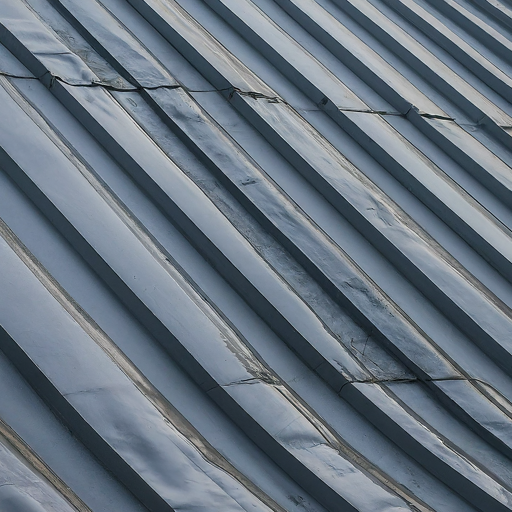
- Types: Standing seam, corrugated panels.
- Advantages: Extremely durable, long lifespan, fire-resistant, energy-efficient.
- Disadvantages: Higher initial cost, requires specialized installation, can be noisy in heavy rain.
Tile roofing
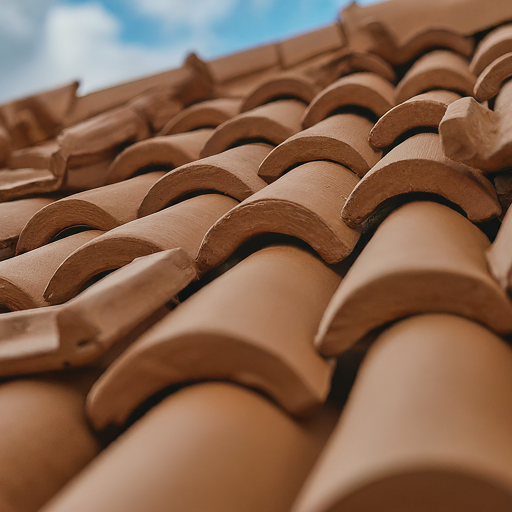
- Types: Clay, concrete.
- Advantages: Aesthetically pleasing, long lifespan, fire-resistant.
- Disadvantages: Heavy, expensive, requires specialized installation, susceptible to cracking.
Concrete roofing
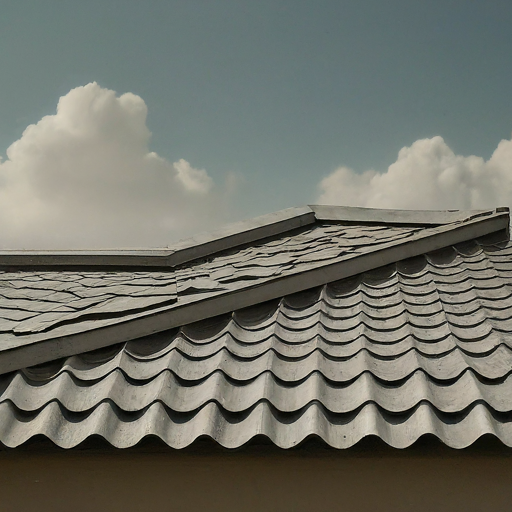
- Advantages: Highly durable, fire-resistant, low maintenance.
- Disadvantages: Very heavy, expensive, requires specialized installation, not suitable for all roof structures.
Solar shingles
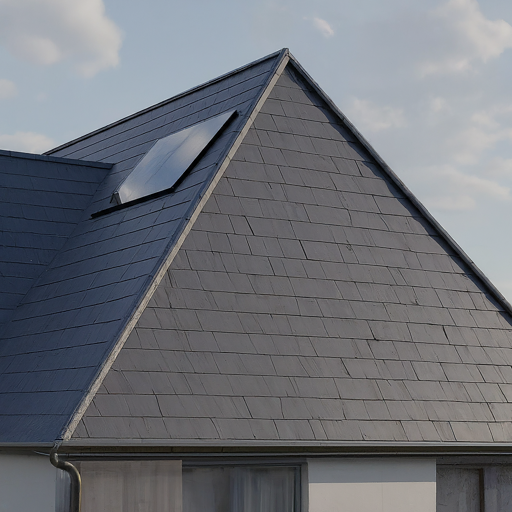
- Advantages: Generates renewable energy, environmentally friendly, potential tax benefits.
- Disadvantages: High initial cost, lower energy output compared to traditional solar panels, may not be suitable for all roof types.
Thatch roofing
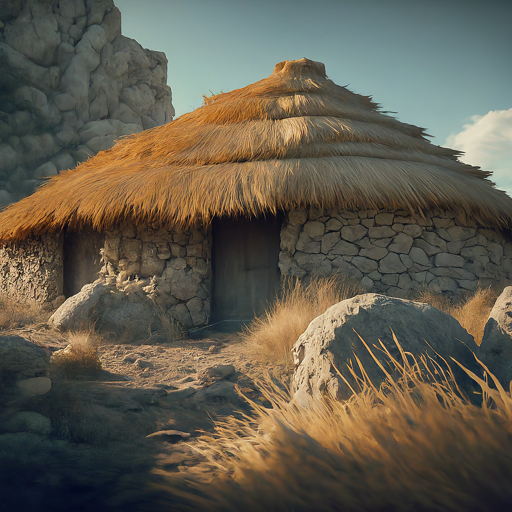
- Advantages: Excellent insulation properties, environmentally friendly, aesthetic appeal.
- Disadvantages: High maintenance requirements, susceptible to fire and insect damage, not readily available in all regions.
Green roofing

- Advantages: Improves building insulation, reduces stormwater runoff, provides habitat for wildlife.
- Disadvantages: Requires specialized installation and maintenance, higher initial cost compared to traditional roofs.
Liquid roofing
- Advantages: Seamless application, good for complex roof shapes, can extend the life of existing roofs.
- Disadvantages: Requires specialized application, susceptible to ponding water, may not be suitable for all climates.
Selection Criteria
Choosing the right technique depends on several factors:
- Building Type: Flat roofs are ideal for membrane roofing, while sloped roofs might favor asphalt shingles or metal panels.
- Budget: Metal and concrete roofing offer high durability but come with a higher initial cost. Asphalt and membrane options are generally more budget-friendly.
- Local Climate: Consider factors like wind, hail, and snow when selecting materials. Metal and concrete roofs excel in harsh weather conditions.
- Desired Lifespan: Metal and concrete roofs offer the longest lifespans, while asphalt and some membranes require more frequent replacement.
- Aesthetics: Tile and metal roofing offer distinct visual appeal, while other options prioritize functionality.
By carefully evaluating these factors and consulting with experienced roofing professionals, you can select the most suitable commercial roofing installation technique for your specific needs and budget.
Step-by-Step Commercial Roofing Installation Process
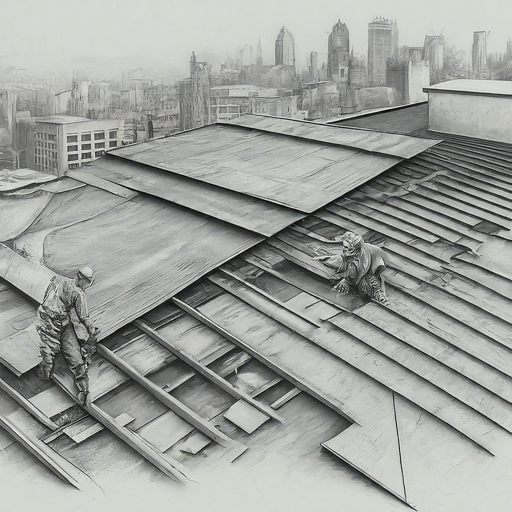
Here’s a breakdown of the key steps involved in a commercial roof installation:
Clearing and Preparing the Site
- Removal of Existing Materials: This might involve stripping off old shingles, membranes, or other roofing components.
- Debris Removal: Ensuring a clean and clear work area for the installation process.
- Roof Deck Inspection: Identifying and addressing any structural damage or weak spots in the underlying deck.
Installing the Underlayments and Insulation
- Underlayments Installation: Applying a waterproof barrier like an ice and water barrier or synthetic felt to protect the roof deck from moisture infiltration.
- Insulation Installation: Adding insulation boards or spray foam to improve energy efficiency and regulate building temperature.
Application of Roofing Materials
- Single-ply Membrane Roofing: This involves mechanically attaching or fully adhering the chosen membrane sheets (TPO, EPDM, PVC) to the roof deck.
- Metal Roofing: Installing panels (standing seam or corrugated) using specialized fasteners and ensuring proper ventilation.
- Other Roofing Materials: The specific application process varies depending on the chosen material (asphalt shingles, tile, etc.).
Flashing Installation and Sealing
- Flashing Installation: Applying waterproof flashing around penetrations like vents, pipes, and roof edges to prevent water leaks.
- Sealing: Using sealants and tapes to ensure watertight connections between all roofing components.
Finishing Touches and Quality Checks
- Cleanup: Removing any debris and ensuring a clean work area.
- Final Inspection: Conducting a thorough visual inspection to identify any installation errors or potential issues.
- Warranty Registration: Completing necessary paperwork to activate the roof’s warranty.
Remember, this is a general overview, and specific steps may vary depending on the chosen roofing system and local building codes. It’s crucial to rely on experienced roofing professionals who follow industry best practices and ensure a high-quality, long-lasting installation.
Post-Installation Maintenance and Inspection: Safeguarding Your Investment
Investing in a high-quality commercial roof installation is only the first step. To ensure its optimal performance and longevity, a robust maintenance plan is crucial.
Here’s why regular maintenance is essential:
- Early Detection of Problems: Regular inspections and maintenance help identify minor issues before they escalate into costly repairs or roof failure.
- Extended Lifespan: Proactive maintenance helps prevent premature deterioration, maximizing the lifespan of your roof investment.
- Improved Energy Efficiency: Addressing issues like clogged drains or damaged insulation can optimize energy consumption and reduce utility costs.
- Reduced Repair Costs: Early intervention prevents small problems from snowballing into expensive repairs down the line.
Schedule for Inspections and Repairs
- Inspections: The National Roofing Contractors Association recommends bi-annual inspections, ideally in spring and fall after harsh weather conditions.
- Maintenance: Address any identified issues promptly to prevent further damage. This might involve minor repairs, cleaning, or recoating.
Tips for Prolonging Roof Lifespan
- Regular Cleaning: Remove debris like leaves, branches, and dirt that can trap moisture and promote deterioration.
- Clear Drains and Gutters: Ensure proper drainage to prevent water pooling and potential leaks.
- Address Flashing Issues: Regularly check for cracks or damage around penetrations and address them promptly.
- Trim Overhanging Branches: Trees rubbing against the roof can cause damage; maintain a safe distance.
- Professional Maintenance: Schedule periodic inspections and maintenance by qualified roofing professionals.
- Warranty Compliance: Adhere to the manufacturer’s warranty guidelines for maintaining the roof’s coverage.
By following these practices, you can significantly extend the lifespan of your commercial roof, ensuring it continues to protect your property and occupants for years to come. Remember, a well-maintained roof is a wise investment that saves you money in the long run and provides peace of mind.
Conclusion: A Durable Roof Starts with a Meticulous Installation
A well-installed commercial roof is an investment that safeguards your property, occupants, and business operations for years to come.
Here’s a quick recap of the key points:
- Planning and Preparation: Thorough inspection, material selection, and permit acquisition lay the foundation for a successful project.
- Safety Measures: Prioritizing safety protocols protects workers and ensures a smooth installation process.
- Installation Techniques: Choosing the right technique (membrane, metal, asphalt, etc.) depends on factors like building type and budget.
- Step-by-Step Process: Each stage, from site preparation to flashing installation and final inspections, is crucial for a high-quality outcome.
- Maintenance and Inspection: Regular maintenance and inspections extend the lifespan of your roof and prevent costly repairs.
Remember, the expertise of experienced professionals is vital throughout the entire process. Hiring qualified roofing contractors ensures adherence to industry best practices, code compliance, and the use of proper installation techniques.
By prioritizing a meticulous commercial roof installation, you invest in a durable, reliable roof that protects your property and provides peace of mind for years to come.